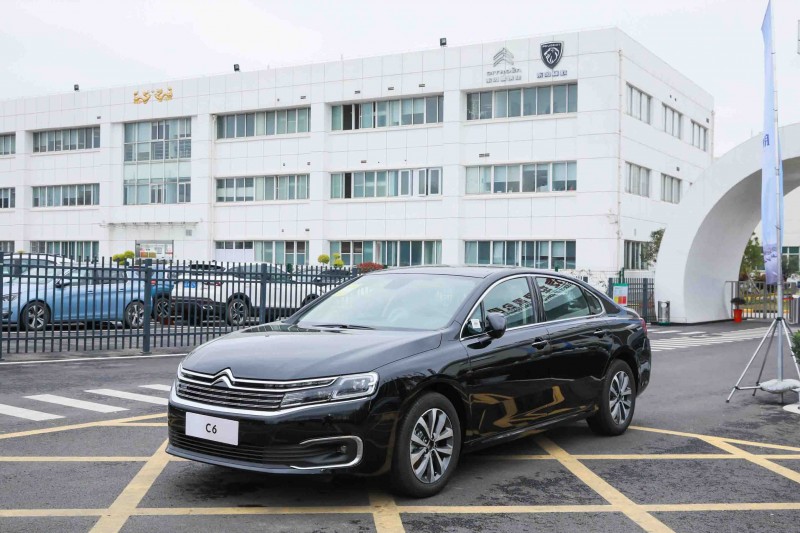
神龙汽车武汉工厂秉承“科技、绿色、精益”设计理念,是Stellantis集团 “全球新一代精益化绿色标杆工厂”,同时也是Stellantis集团和东风公司最先进的、管理绩效指标最好的工厂之一,曾连续两年获得Stellantis集团全球工业领域“金棕榈——最佳工厂”大奖,同时,还以卓越的质量和安全工作获得Stellantis集团“全球工业领域最佳整车工厂”、质量“工业奖”和安全“工业奖”。
神龙公司武汉工厂具备坚实的造车底蕴、精益管理的深厚沉淀、领先的工艺水平、严谨的质量控制体系,以及高素质员工队伍的保障,这些都将为东风雪铁龙、东风标致的制造质量保驾护航。
1、冲压工艺
冲压工艺上,冲压车间的2000T压机采用德国博世-力士乐的数控液压拉伸垫技术,在冲压加工中,尤其是复杂的几何外型加工中,保证了高度精确的工艺控制,提供了高效、高性能、高质量的冲压件。
冲压线采用先进的机器人自动化技术,实现了快速和可靠的零件输送,生产效率高,最高生产节拍达到12件/分钟。EMP车身线集成了自动涂胶工艺设备、车身成型机、顶盖激光钎焊工艺设备等国内先进水平的工艺及设备。
2、焊接工艺
神龙公司武汉工厂拥有FANUC和MOTOMAN机器人320台以及ALW激光焊接设备等先进设备、并在国内首次运用CMT冷弧焊工艺,广泛使用3G模块化焊钳和中频焊接技术。CMP平台设备自动化率80%,PF2平台设备自动化率72%,PF3平台设备自动化率45%。
3、涂装工艺
神龙公司武汉工厂是世界上首家同时采用绿色前处理+短工艺+水性漆的工厂,而且配置有2台6轴机器人用色差仪、红外线反射波、超声波等仪器,100%检查漆面色差、平滑度和膜厚,并配合100%人工检查。
这不仅使涂装VOC排放处于国内领先水平(仅为20g/m2),支持国家环保事业。而且更为有力的保证了漆面质量,确保油漆外观靓丽耐久。TTS-CATA采用绿色前处理硅烷技术,面漆采用免中涂短工艺,利用先进的绿色硅烷技术、免除中涂生产环节,在防腐性能保证上丝毫没有降低,同时还节省了能耗。
4、总装工艺
总装车间在规划设计上广泛运用了新技术、新材料、新工艺。总装生产线采用数字化的防错技术及柔性生产技术,确保产品的质量和灵活性,前驱、后驱和四驱车型均可以共线生产,可轻松实现PDI专属定制服务,包括劲浪音响、双层夹胶玻璃等从前只有高配车型才提供的装备。专属定制为客户提供了丰富的选择,极大地满足了车主多样以及个性化的需求。
为了给用户提供最好的产品质量和最高的客户满意度,总装车间采取了极为严格的质量控制措施,主要包括采用的140余台伺服拧紧机,拧紧力矩精度达到0.01NM,角度精度偏差小于1度,全方位保护用户安全;分布在总装各区域的五个质量门,在制造过程中严控质量;93%的集配率,从源头杜绝错漏装缺陷的产生;严密的零件追溯系统,让用户的用车放心。
5、质检工艺
在质检工艺上,神龙公司武汉工厂的专业检查人员会对每台车辆进行20道工序的检查,并模拟300多项用户操作,100%确认车辆的外观、功能、密封合格。
其中,一些检查项目也是非常专业和先进的,包括:
模拟12种复杂路面驾驶的动态跑道试验,检测驾驶性能和舒适度。
实施100%高精度电子电气检测,通过20余项全自动电检,保证各项车载电器功能性。
进行底盘功效检测(即转毂试验),模拟检测0-130KM/H的动力性,并测试脚刹、ESP制动、手刹等各项制动性能。
134年造车底蕴,神龙汽车旗下东风雪铁龙、东风标致主销产品,高强度钢板占比最高达80%以上;六横六纵太空舱结构;60余位全国劳模、工匠大师的匠心制造;1100多项整车测试验证;5000多个焊点质量循环监控;546项功能安全或失效场景管控,守护客户一生安全。
据权威机构数据显示,神龙汽车产品的事故车辆损害程度仅为行业平均的64%;被大家称为“撞不坏的法系车”“保命的法系车”。
看得见的是价格和热度,看不见的是品质和服务”。东风雪铁龙、东风标致补贴背后的良心品质和五心服务的认知,让外界了解神龙坚持“长期主义”的决心不变,在产品、技术、品牌营销等方面,都拥有清晰的规划。并且还将客户关系从“买卖”升级到“知音”,为客户提供“品质知音”“服务知音”“生活知音”三大价值,持续提升用户体验。